ドイツ・ぺリンガー社訪問記 |
WORKERSで初めて革財布を作るにあたり、どうしてもこの革を使いたい!と思ったのがドイツ・ぺリンガー社のノブレッサカーフ。
ぺリンガー社の革は、ルボナーさんの製品でもたくさん見てきましたが、その中でも私が好きなのがあえてシュランケンカーフではなくノブレッサカーフ。固い、型押しをした革。クローム鞣しで固い、型押しというといかにも経年変化が少ないように思いますが、さにあらず。
財布はもちろん、ぺリンガーの固い型押し革が靴にも使われているようで、その経年を見ても素晴らしいもの。適度に腰が出て、表面の型押しは徐々につぶれていく。でも、やはりクロームらしい「ピン」とした新品の風合いも残る。
せっかく、そんな革を使わせてもらうなら!と2017年10月、ドイツとチェコの国境近くにあるぺリンガー社を訪問してきました。
|
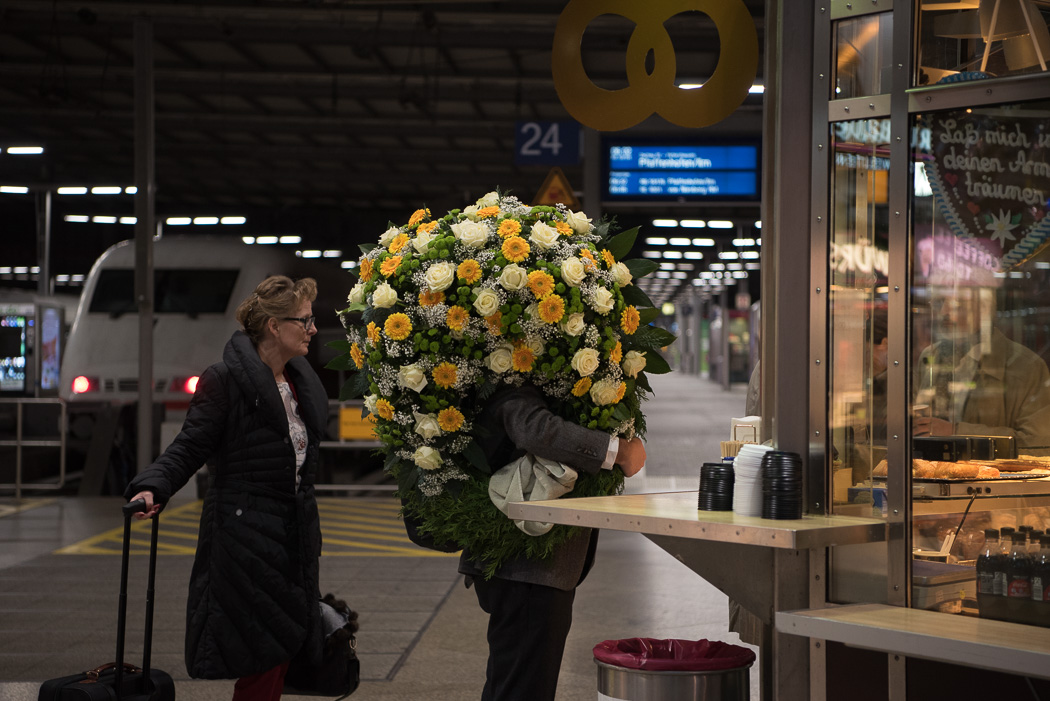 |
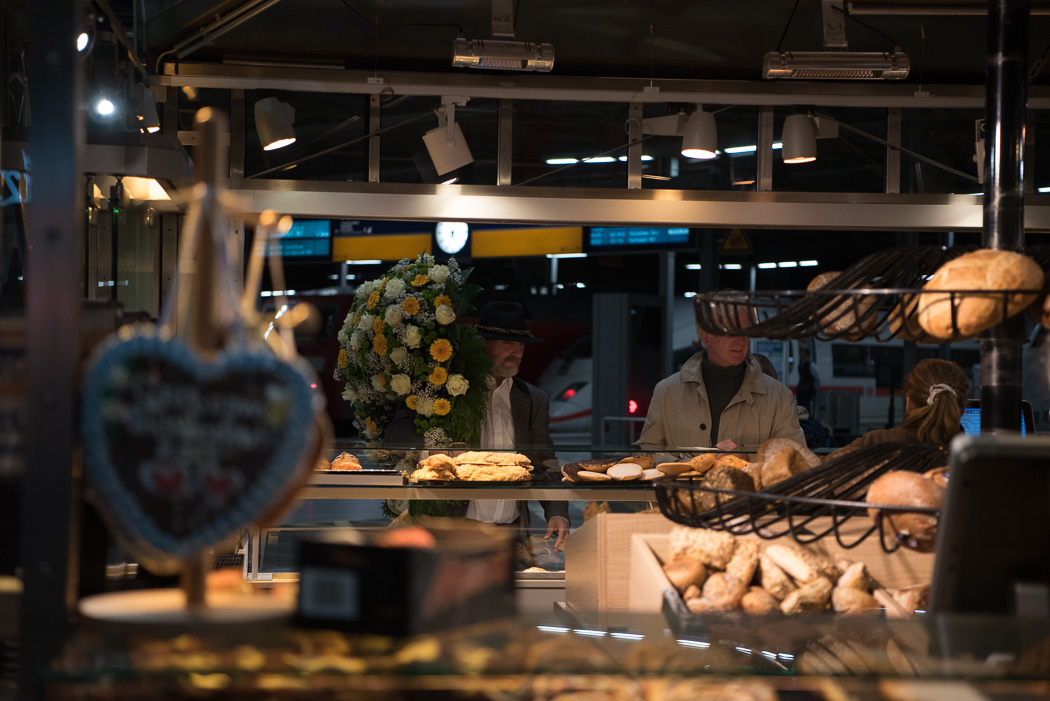 |
ミュンヘン中央駅・朝6時に花抱えたイカしたおじさん。
|
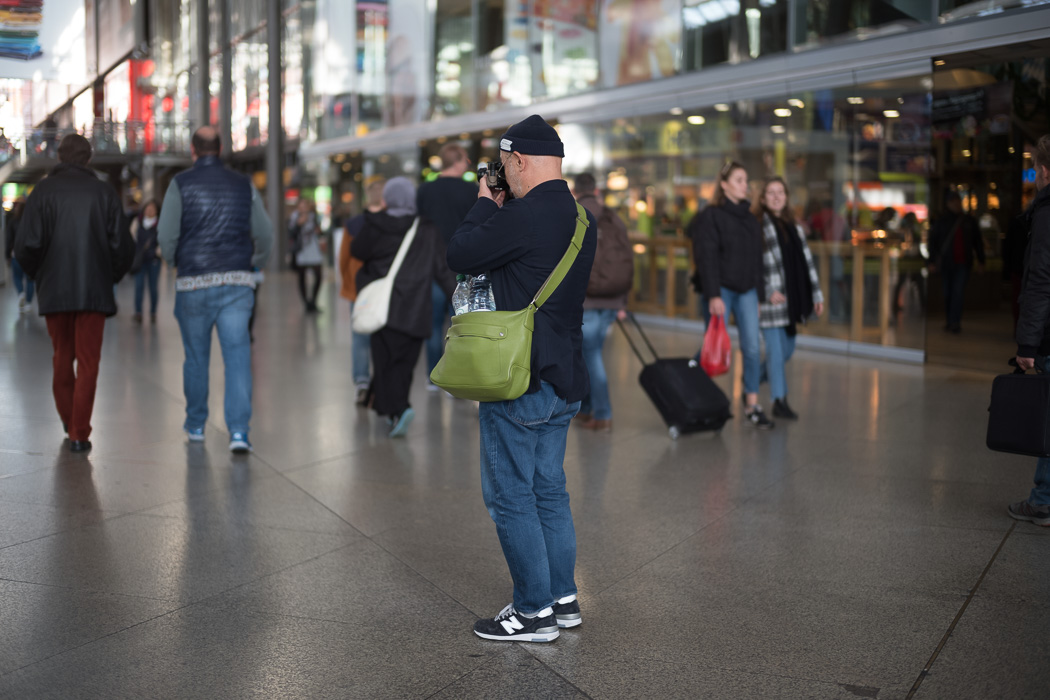 |
もちろん、おなじみのおじさん に連れて行ってもらいました。
皆そろったところで、ミュンヘンからアウトバーンを150キロですっ飛ばしぺリンガー社へ向かいます・・・
|
|
|
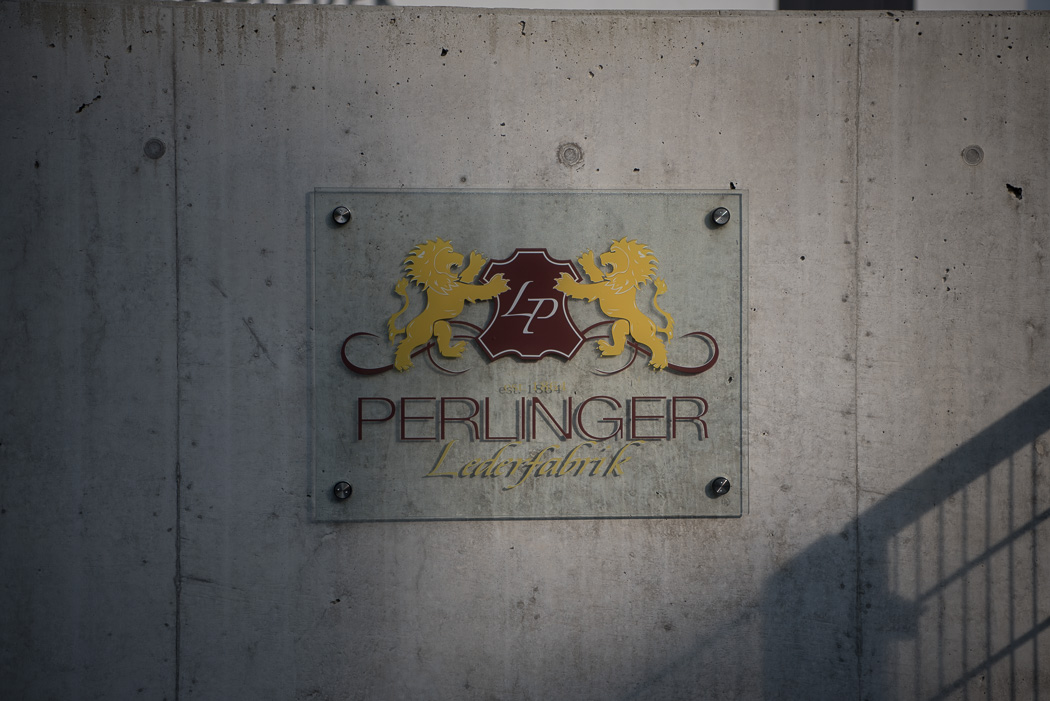 |
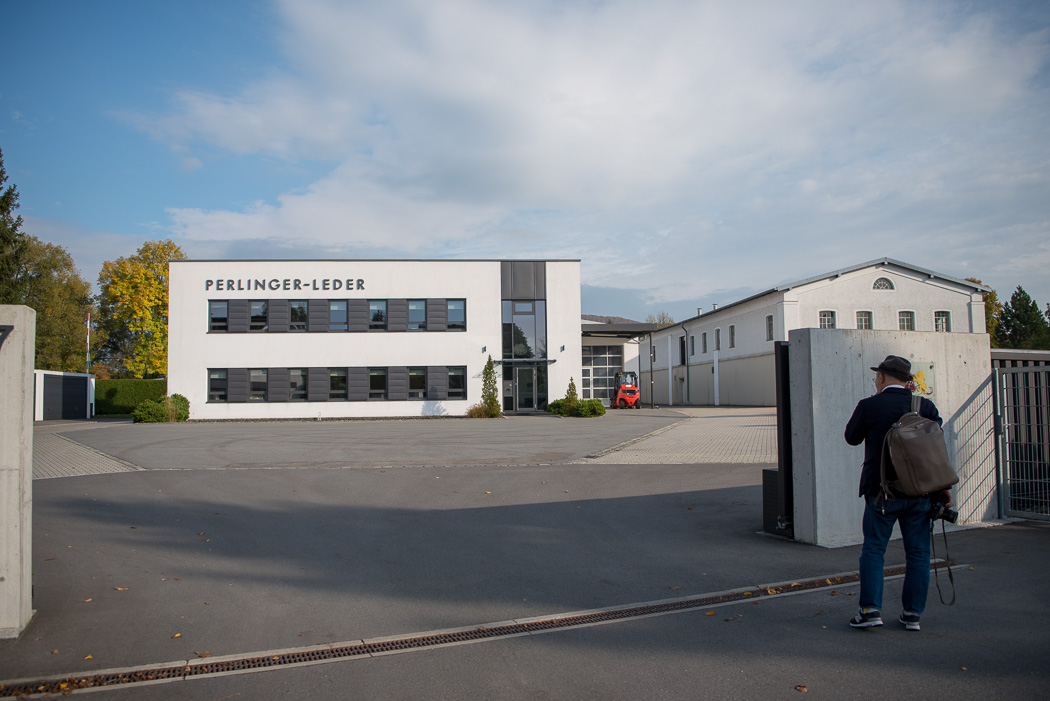 |
早速ですが、ぺリンガー社全景。チェコとの国境近くにぺリンガー社はありました。
現在は周りに家々も立ち並んでいますがもともとは街はずれ。どうしても、製造業は排水の問題もあり、はるか昔にここに移転してきたそうです。
日本の紡績工場(糸工場)でも「もともとは駅前でやってたのが、火事もあって移転して、家もないから大丈夫と思っていたら周りに家が今では建って・・・」とまったく同じ話を聞いたことがあります。
全体像としては「とにかくきれい、そして小さい」。このイメージは中に入っても変わりません。
|
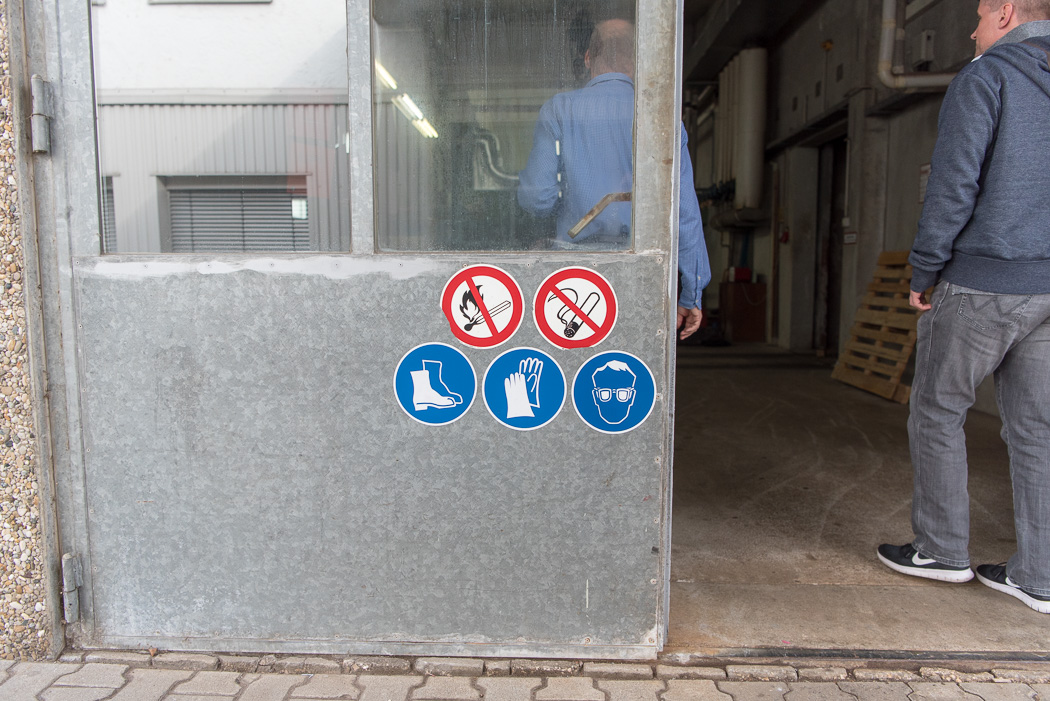 |
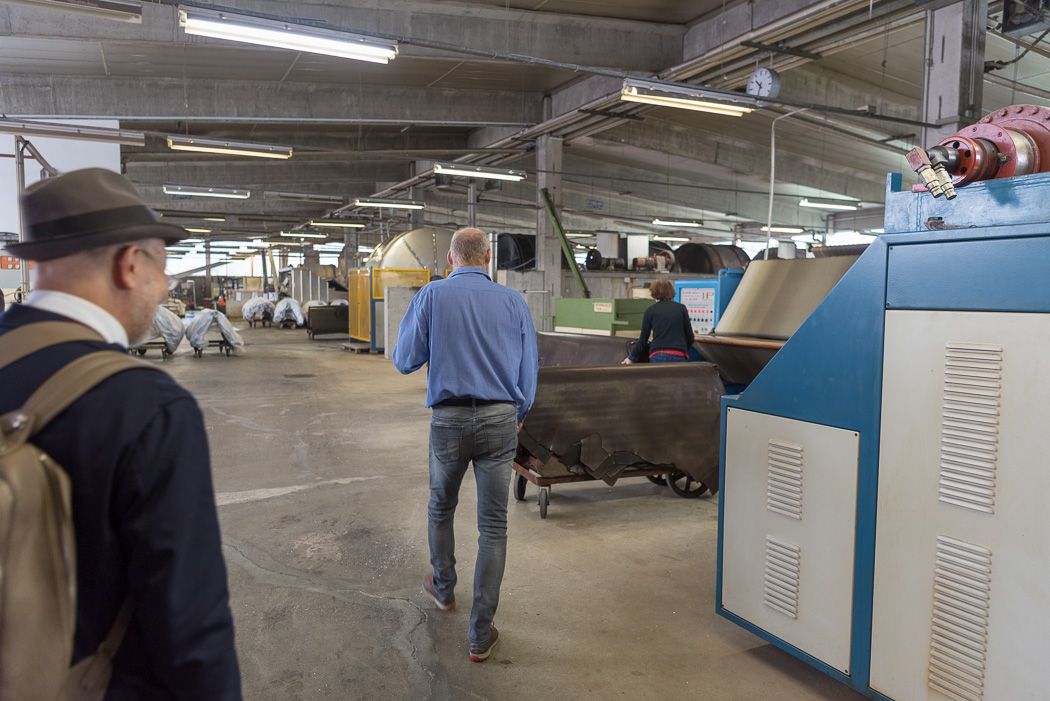 |
案内してもらったのはぺリンガー社社長。代々、社長をされているそうです。革に対する情熱はもちろん、経営も熱く語っていました。印象的だったのが
「Small is the best」
ぺリンガー社では、プレミアムな革をクオリティ重視で作りたい。そうすると、結果として少量しかできない。なので、クライアントは小さければ小さいほど良い。例えば「何千足の靴を作りたいから、その革をすぐに用意してくれと言われても出来ない」WORKERSも一人ですと言ったら「それが良い、プレジデント to プレジデントで話ができるのが一番良い!」と。
工場に入って一番に感じたのが
「匂いがしない」
どうしても、革をなめす工程は、使う薬品の匂いがしたりするのですが、ぺリンガーの工場はほとんど匂いがしませんでした。そして、ぱっと見てわじゃるますがとにかく工場がきれい。整理整頓され、使い込まれた道具たち。これぞ「正しい工場」という姿です。
|
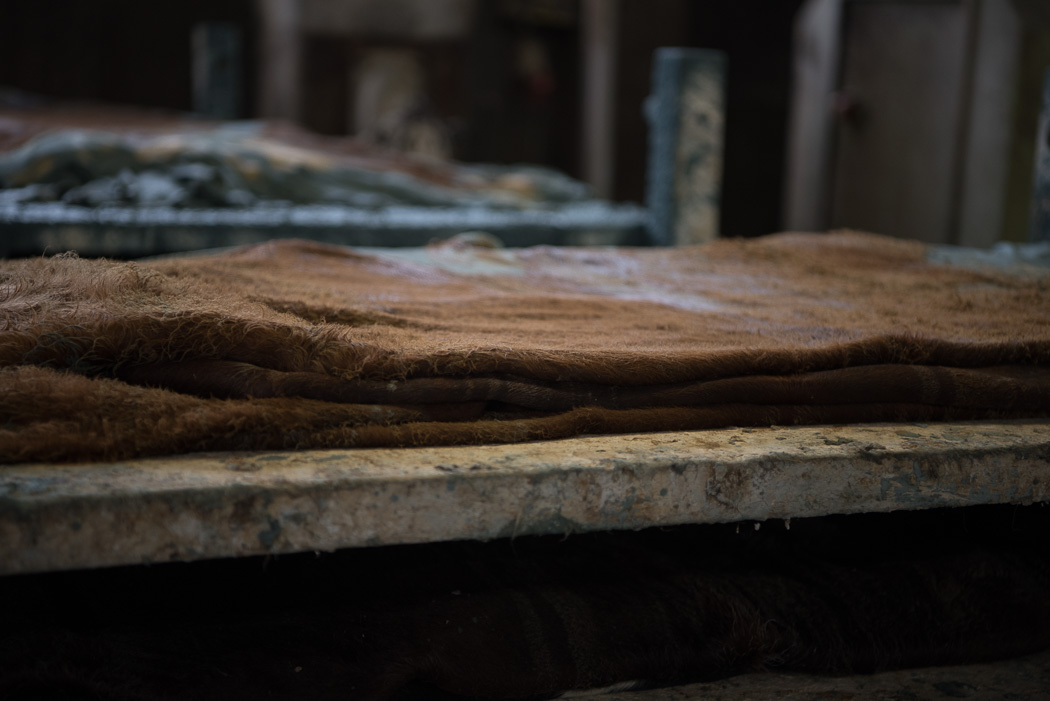 |
原皮は毛がついた状態で納品されます。まずはこの毛を取る事から鞣しがスタート。ここでも、日本で良くある石灰ではなく硫黄を使って毛を取っているそうですが、いわゆる硫黄の匂いもほとんどしませんでした。日本の硫黄と何か違うのだろうか?
|
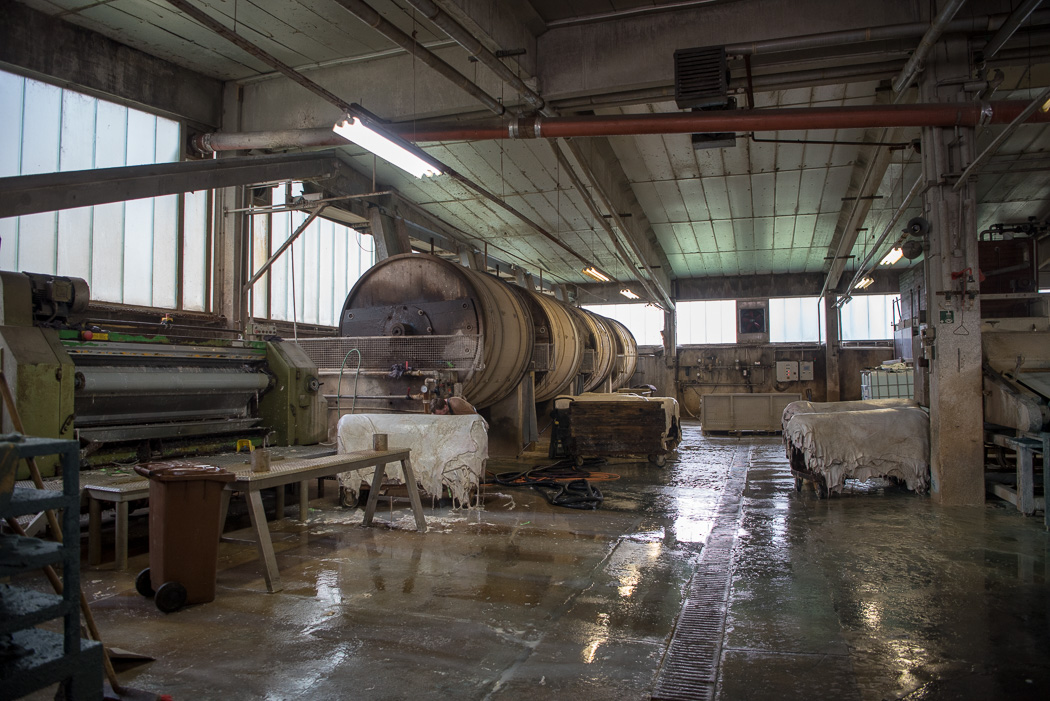 |
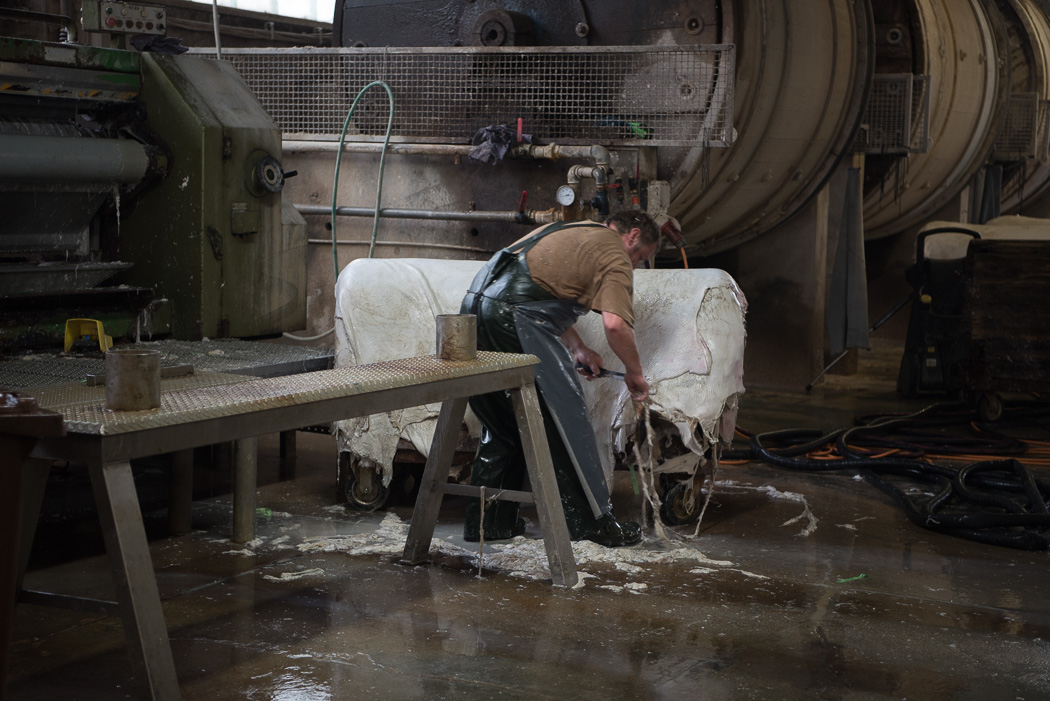 |
毛を取り、さらに革になるには余分な部分を取るための洗い工程。この工程から、どんどん端の方の余分な部分はカットしてしまっているのを見ました。
革は通常「デシ」という面積で価格が決まります。単価×デシで一枚の値段が決まります。なので、作る側とすれば本来は革が大きければ大きいほど売り上げが上がる。それでもぺリンガー社では、使えないと判断した部分はどんどん切り落としていました。これ、できそうでできないことなのです。クオリティ重視というのが一番直接感じられる部分です。
写真が見切れてしまいましたが、この後、右側にあるタイコでいわゆる「ウェットブルー」と呼ばれるすっぴんの革になめしていく工程があります。
ウェットブルーになって初めて、革の素性が見えてくる。あるものは厚みがあり柔らかい、あるものは薄めで固い。またあるものは、残念ながら傷が多い。
そこで選別が行われ、これはノブレッサカーフ、これはシュランケンカーフ。傷が多いものは革の銀面(表面)を削ってしまい、靴の中材として使う革に・・・
この選別も厳しくやれば、「この種類の革はこの枚数しかできない」となります。だから「すぐに何千足分の革を」と言われても作れない理由です。
|
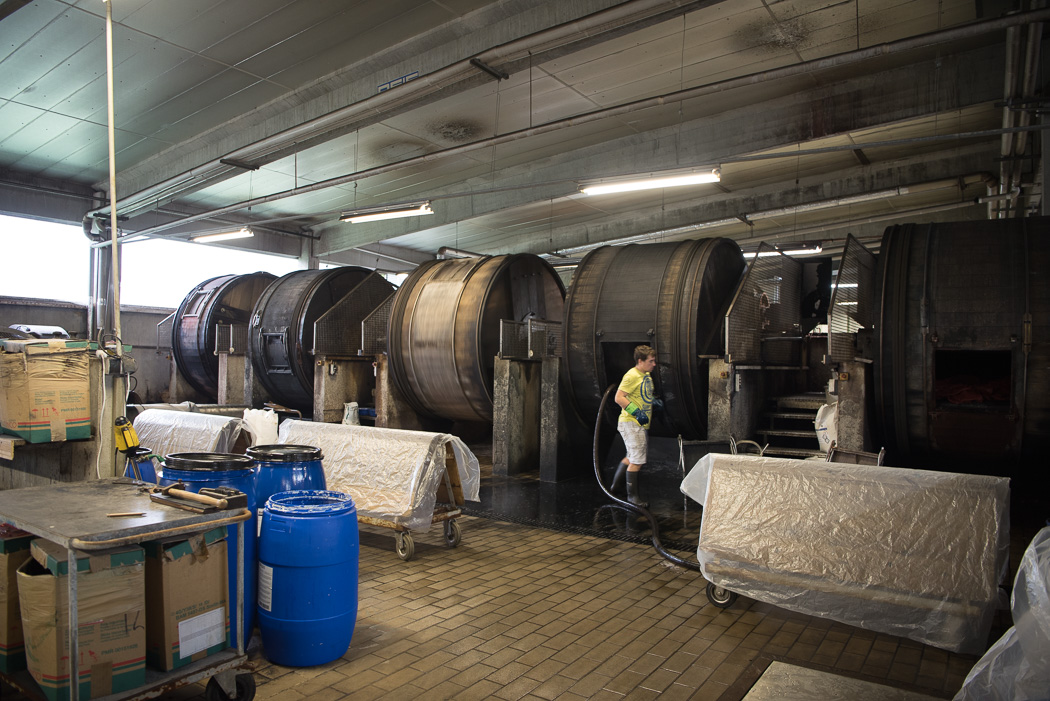 |
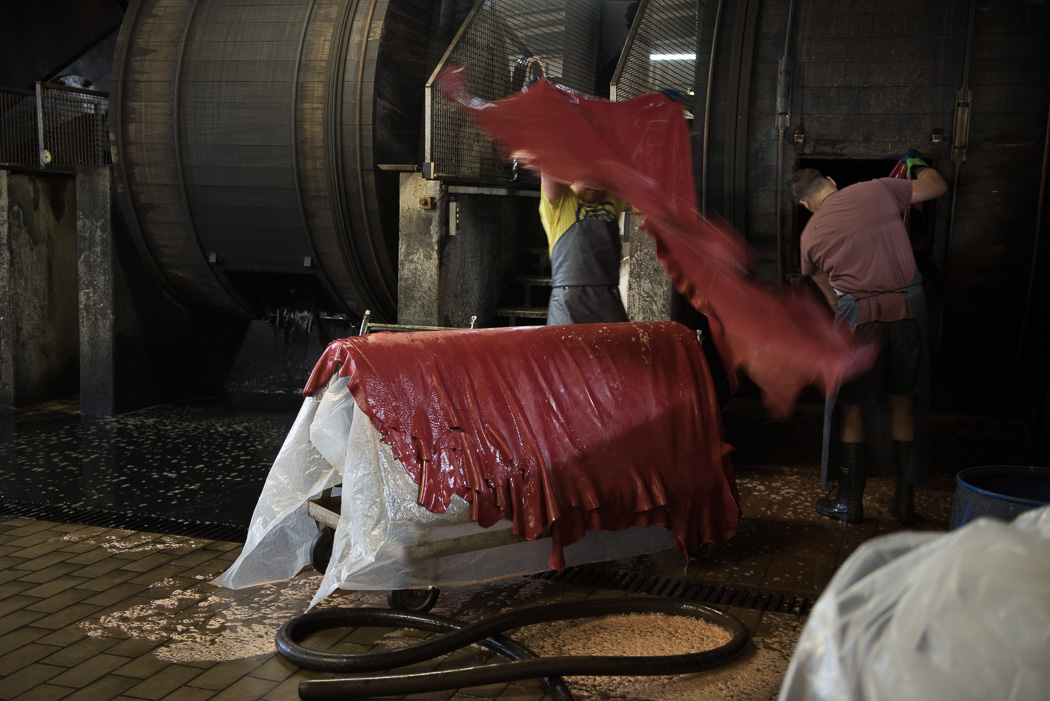 |
ウェットブルーになった革、いよいよ染色しながらさらになめされていきます。最初、この工程は色を入れるだけかと思ったら、ここでもさらに「鞣し」が行われているそうです。あるものは固く、あるものは柔らかく、あるものは薬品でシュリンク(縮めてシボを出し)といったように。たくさん並ぶタイコは「これは黒など色の濃いもの用」「これはブルーなど鮮やかな色」「これは固い革、つまりノブレッサのようなものに」「これは逆に柔らかい、シュリンク革用」といった用途別に並んでいます。
上の写真でもわかるように、一回ごとに使うたび、きれいに洗いはするのですが、どうしても濃い色をやったタイコでは薄い色を後から行くと色がくすむ。それを避けるため、タイコを用途別に使い分けています。
|
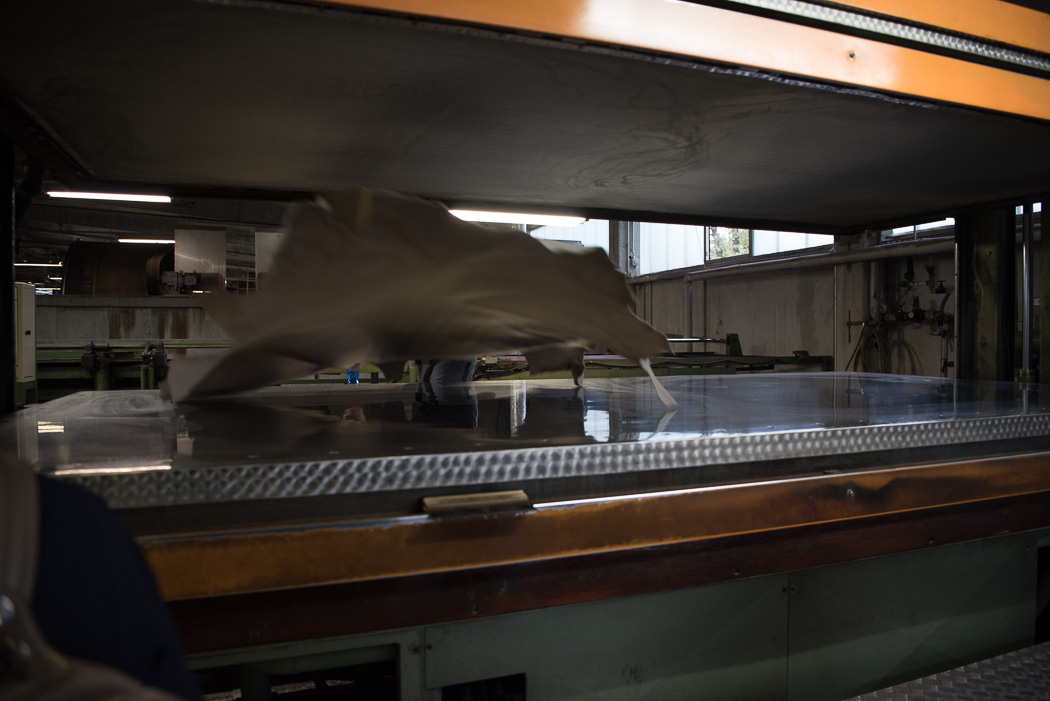 |
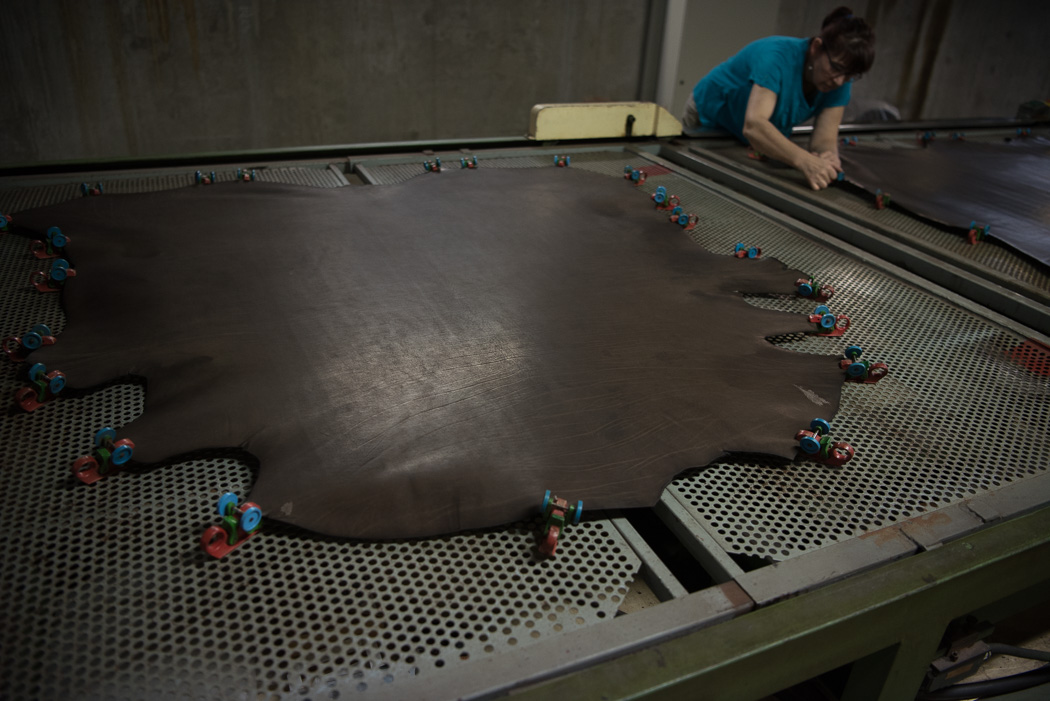 |
タイコでの鞣しが終わった革はさらにいくつかの後加工があります。あるものはアイロンで、あるものはバイブレーション(ぶるぶるふるえさせて)いたり。後加工は数種類あり、最終的な風合いに合わせて種類を組み合わせて行います。
|
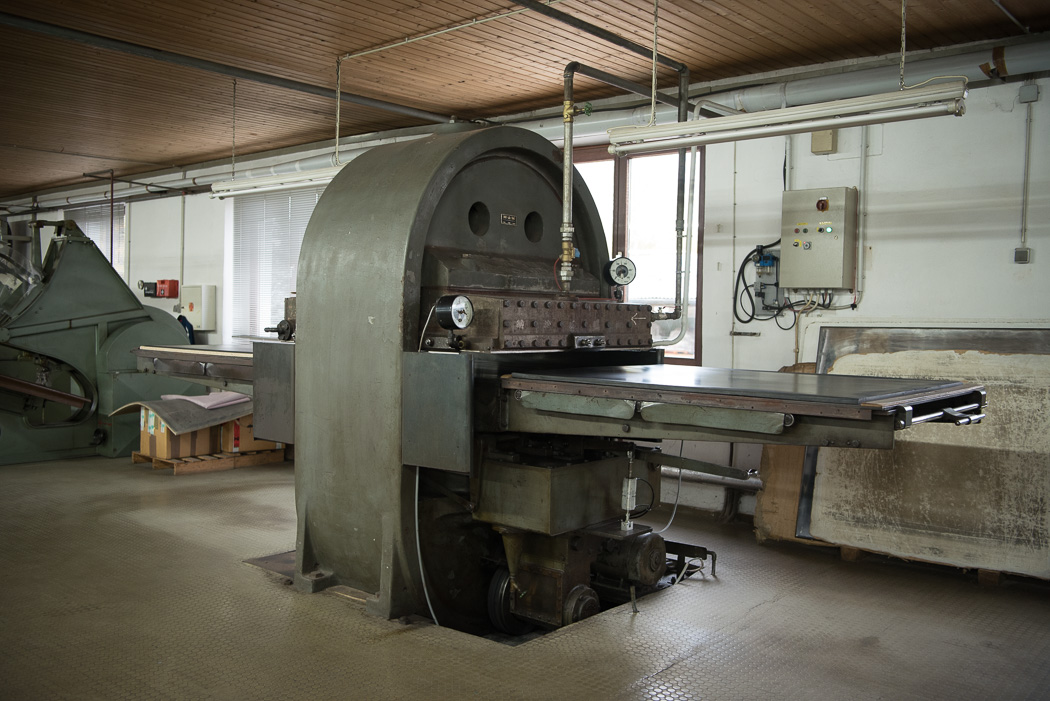 |
そして・・・先ほどの隣の建屋についに発見!!!ノブレッサカーフの型押しをする機械。貫禄十分!これが見たかったのです。ローラーのような版かと思ったら平らなエッチングのような版でした。
|
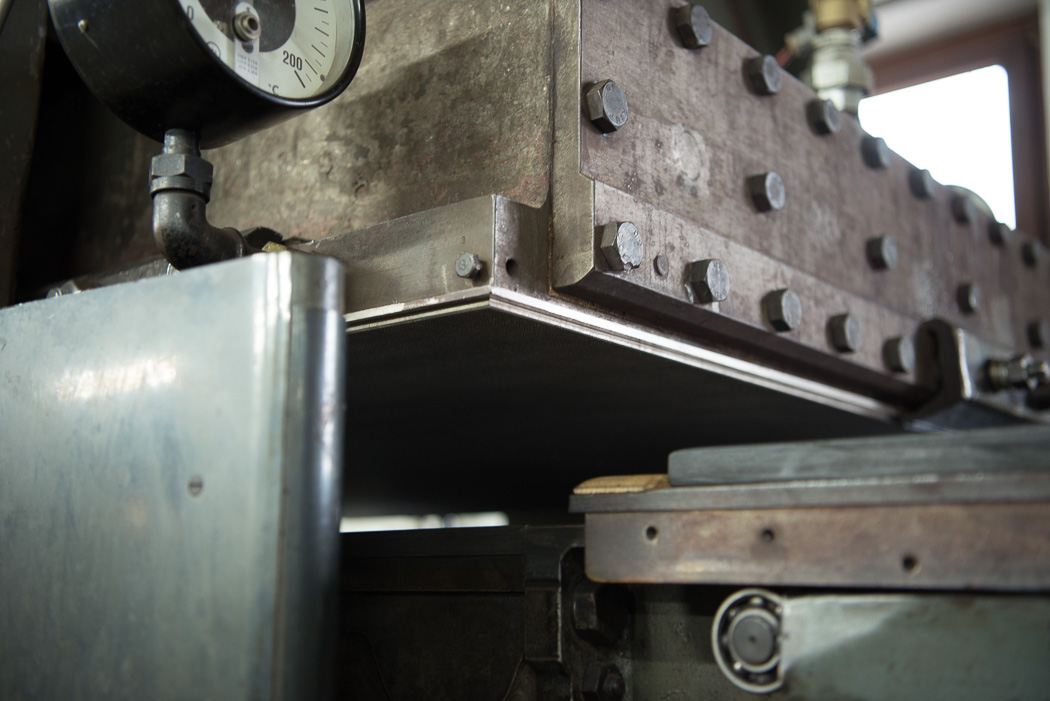 |
機械の上側には型押しの版が固定されています。これがどしんと下に落ちてきて熱と圧力で型がおされるのですが・・・
|
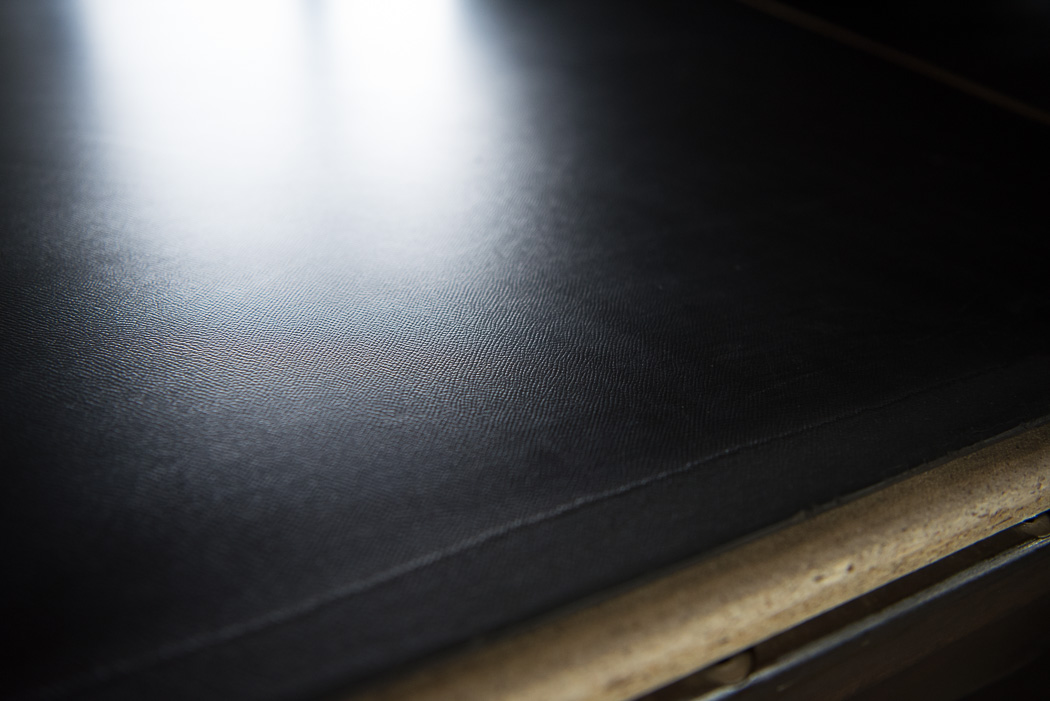 |
押される側のマット。おそらく、圧力調節でカラ打ちをするのでしょう。型押し版の跡がくっきりとついています。
|
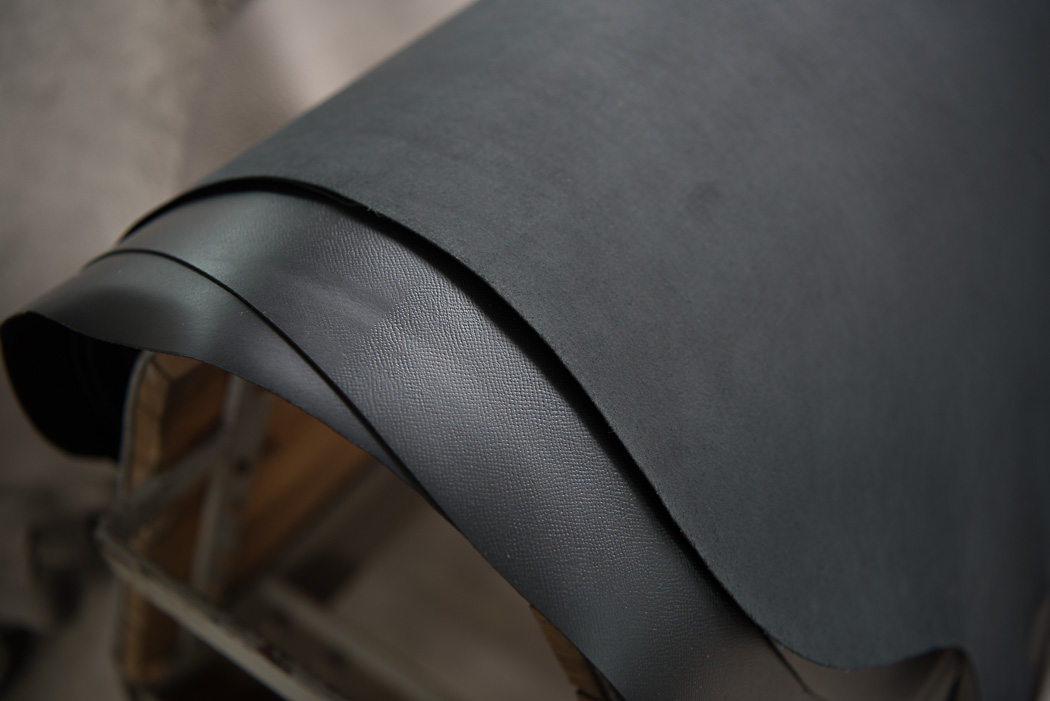 |
そして出来上がったノブレッサカーフがちょうど出荷を待っていました。型押し版の大きさは限りがあるので、真ん中は版が二度押された状態になっています。ここれは製品を作るときは使えない部分。
工場見学してわかったのが、とにかく量より質。すべての工程をきれいな工場で、でも人の手と、目で時間をかけて。各工程でいちいちチェックしたり、余分な部分を落としたりしながら、気を使って作業しているのがわかりました。後は経験。過去の膨大なデータが保管されているのも確認できました(社長すらあまりに膨大で細かいことは担当者にしかわからん!と言ってましたが)
ぺリンガー社自体、100年以上前はシブ鞣しをしていたそうです。それが、当時の社長がカナダにクローム鞣しの勉強をしに行って転業したそうです。使う側は「この革いいよな〜」と言うぐらいですが、その「いいよな〜」には長い年月や人の人生がかかってるのだな・・・と再確認する旅でした。
|